The different types of steam traps
The availability of a wide selection of steam trap variants frequently leads to confusion regarding the optimal choice for a given application. This confusion arises because all traps essentially perform the same function – evacuating condensate and trapping steam.
However, for a given application, there is only one “right trap choice”.
Therefore, careful consideration should precede the selection of steam traps. To do this, it is necessary to understand that each type of steam trap is characterised by its distinct working mechanism. These diverse working mechanisms enable the traps to differentiate between steam, condensate and air and each has its own set of advantages and limitations which need to be considered while making the choice.
Steam traps can be broadly classified into three primary types based on the principle of operation: kinetic energy operated thermodynamic steam traps, density operated mechanical steam traps and temperature operated thermostatic steam traps.
Thermodynamic Steam Traps
These steam traps operate on the principles of thermodynamics, i.e. based on the difference in velocity between flash steam and condensate. Thermodynamic traps consist of a single moving part i.e. a specially designed disc that rises to permit the discharge of condensate, and closes against a seat to prevent the passage of steam through the trap.
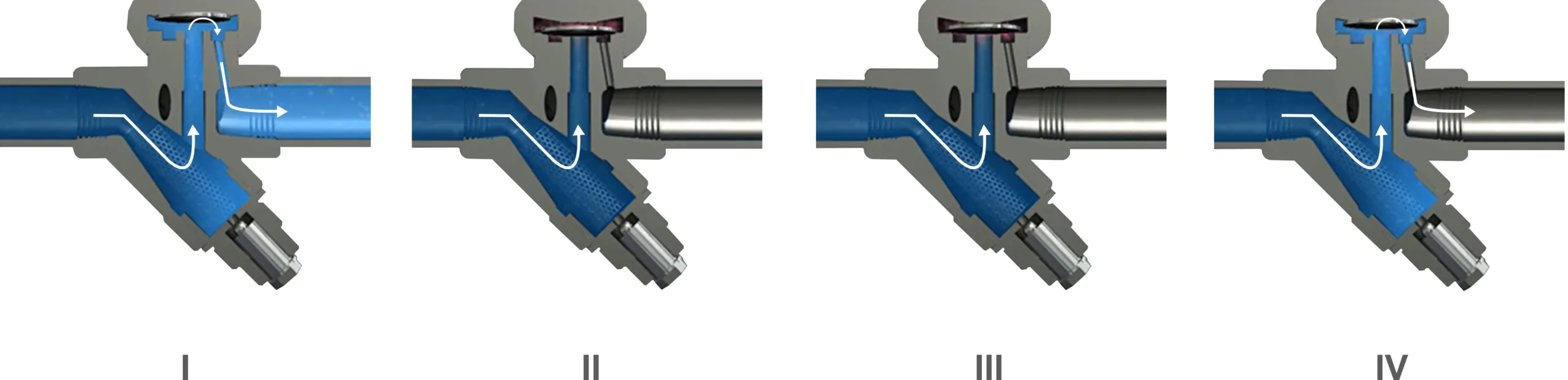
Illustration: How thermodynamic steam traps work
- At startup, the incoming pressure raises the disc, allowing air and subcooled condensate to be discharged through the trap.
- As hot condensate enters the trap at high pressure flash steam is generated due to a drop in pressure. This flash steam moving at a high velocity, creates a pressure drop under the disc. Concurrently, the flash steam accumulates above the disc, exerting downward force.
- These combined actions lead the disc to seal against the seat.
- As the flash steam above the disc condenses, the pressure from the condensate causes the disc to lift again, allowing condensate to be discharged through the trap. This cycle is repeated.
Thus thermodynamic steam traps discharge condensate intermittently. While this makes them unsuitable for process heating applications, they are considered to be the best choice for removing condensate from steam distribution pipelines as they have several advantages over mechanical and thermostatic traps.
Being more compact, in comparison, radiation losses from the trap are significantly lower. This is particularly important since distribution traps are installed at 30 meter intervals and can add up to a significant number in any plant. Moreover, they are compatible across a wide pressure range, and are robust and easier to maintain as they have just a single moving component. Thermodynamic steam traps are also able to withstand water hammer and corrosion and are better suited to work in areas prone to sub-zero temperatures as they are resistant to freezing.
Density Operated-Mechanical Traps
These traps use mechanical mechanisms that rely on the difference in density between condensate and steam, to facilitate their opening and closing. As these traps open and close only on the basis of the density difference between condensate and steam, their performance is not affected by the surrounding environment. Float traps and inverted bucket traps are the most widely used mechanical traps operating on this principle.
Ball Float Traps
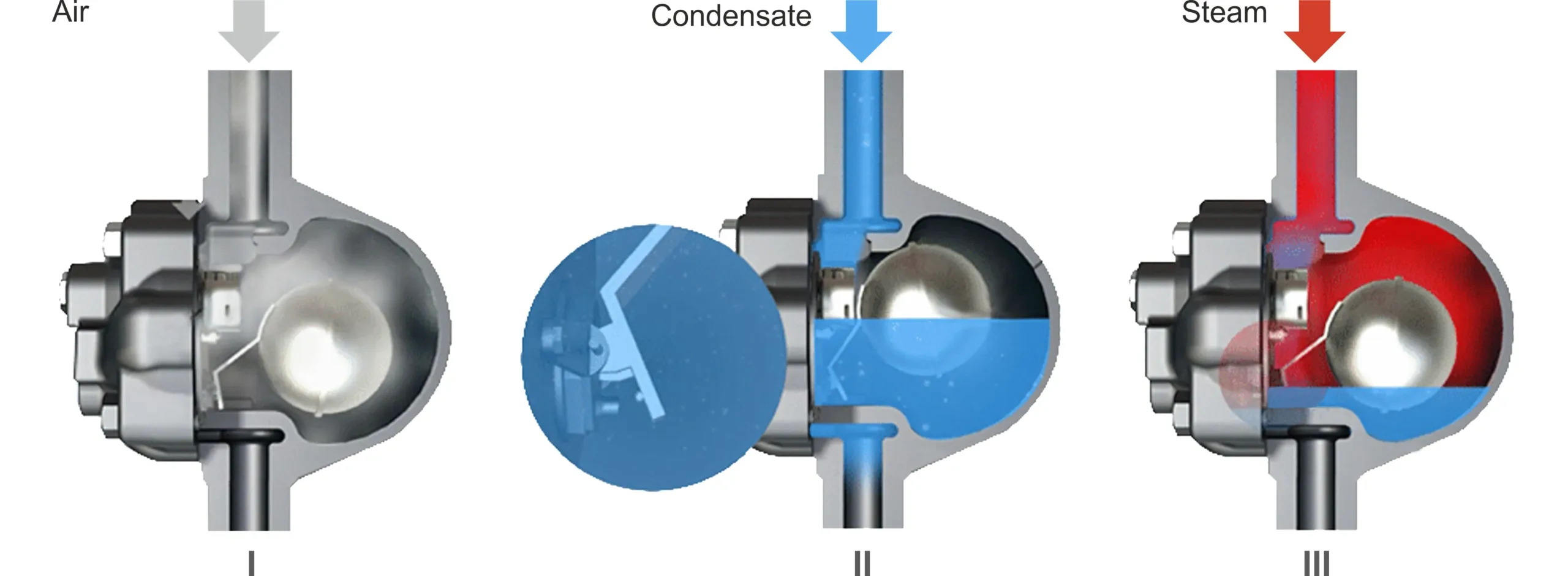
Illustration: How ball float steam traps work
A ball float trap or float trap as it is commonly known, uses a float mechanism to open and close a valve in response to the level of condensate in the trap.
- At start-up, the thermostatic air vent allows air to be evacuated from the system. Removing air and other non-condensable gases is essential as they hamper heat transfer.
- As condensate enters the trap, the float rises on account of buoyancy, the lever mechanism opens the main valve enabling condensate discharge.
- When steam enters the trap the float drops, closing the main valve.
By virtue of this operating principle, float traps modulate with the condensing rate, discharging condensate continuously and hence are ideal for process heating applications as they evacuate condensate from the equipment as soon as it is formed. These traps are designed in such a way that the valve seat is always submerged under water preventing any steam loss.
Ideally, for process applications, ball float type steam traps are the best choice due to their continuous discharge characteristics.
Inverted Bucket Steam Trap
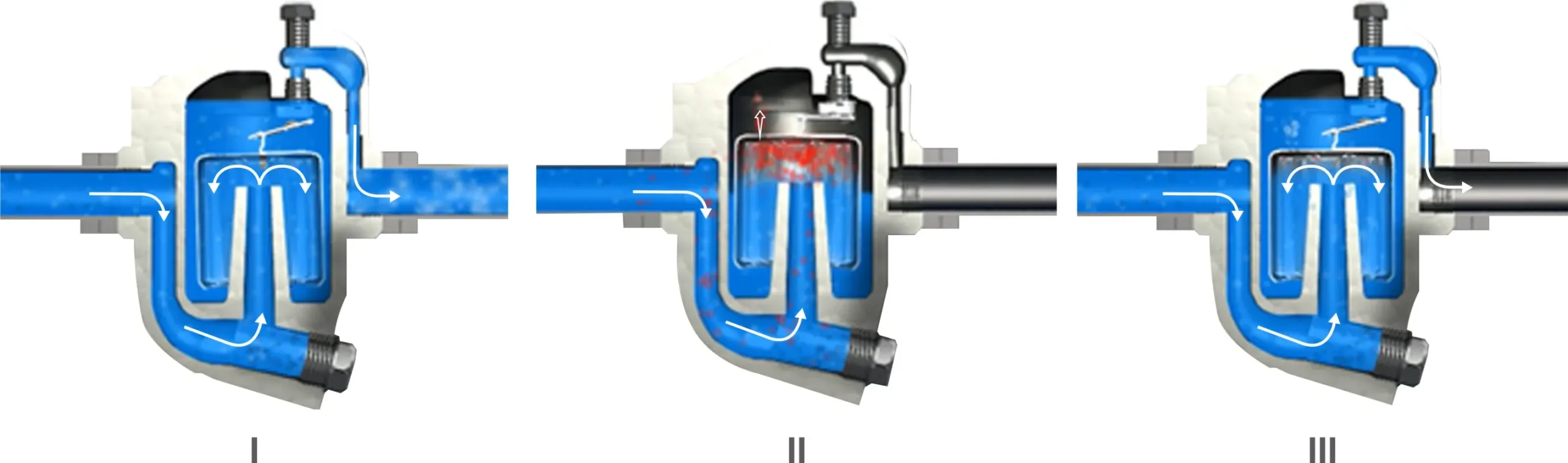
Illustration: How inverted bucket steam traps work
This type of trap uses an inverted bucket as its operating mechanism. The bucket is connected to a lever that opens and closes the trap outlet valve. The trap body is normally filled with condensate to maintain a water seal around the inverted bucket.
A small vent hole is provided in the bucket. This vent hole facilitates the removal of air and non-condensable gases during start-up. However, as the hole is very small, the trap is relatively slow at venting air / non-condensable gases.
- During normal operation, condensate which enters the trap flows under the bottom of the bucket and out through the outlet valve provided.
- As steam enters the trap, the bucket becomes buoyant, rises to the top shutting the outlet valve. The trap remains closed until this bucket-full of steam either condenses or passes through the vent hole provided in the bucket.
- The bucket then drops to its original position once again opening the outlet valve, allowing condensate to be discharged.
In this process, the inverted bucket trap consumes a bucket full of steam to operate. Furthermore since their operation is intermittent, inverted bucket traps cause condensate accumulation in the equipment steam space. This hampers process heat transfer resulting in non attainment of desired temperatures and higher batch times.
Condensate accumulation also leads to water hammer that damages process equipment.
Steam Operated Pumping Trap
In temperature controlled processes where process temperature requirements are below 100°C, the differential pressure across the steam trap becomes negative. This occurs when the heat load of the process reduces and correspondingly the steam supply control valve throttles.
Conventional steam traps discharge condensate when the upstream pressure is greater than the downstream pressure i.e. when the differential pressure is positive. However, when the upstream pressure is either equal to or lower than the downstream pressure / backpressure on the trap it will not be able to evacuate condensate.
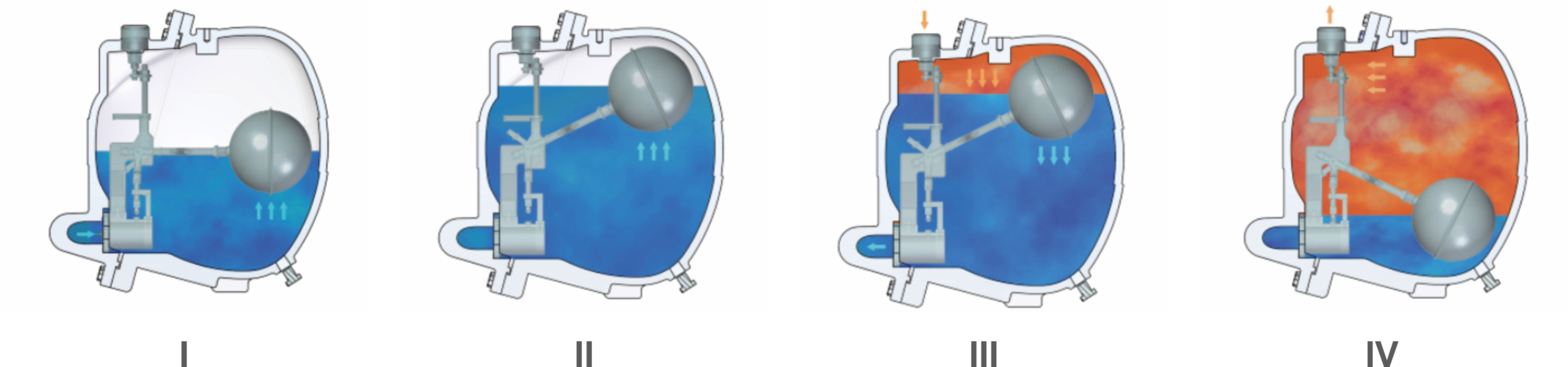
Illustration: How steam operated pumping traps work
- A steam operated pumping trap uses a float mechanism to operate. Under normal conditions it operates like a conventional float trap to evacuate condensate.
- However, when the differential pressure across the trap becomes negative, the trap is unable to evacuate condensate and the level of condensate in the trap rises beyond a specific threshold.
- As the float ascends beyond the specific threshold, it opens the steam inlet valve
- Steam enters the trap and is used as the motive force to pump condensate out.
Thermostatic Steam Traps
These traps work based on the temperature difference between steam and condensate. Thermostatic traps contain a temperature-sensitive element that contracts when it comes in contact with condensate, causing the trap to open and discharge condensate and expand when it comes in contact with steam, closing the trap. There are three types of thermostatic traps i.e. Balanced Pressure, Liquid Expansion and Bimetallic steam traps.
Bimetallic Steam Traps
These traps use a bimetallic element (strip /disc) as the key component, comprising two different metals with different thermal expansion coefficients, bonded together. Due to this differential expansion of the two metals, the strip deforms when it heats and returns back to its original position when it cools. This results in opening and closing of the trap outlet valve facilitating the discharge of condensate and trapping of steam.
Bimetallic steam traps are typically suitable for high temperature steam tracing applications.
Balanced Pressure Thermostatic Steam Traps
Balanced pressure steam traps contain a liquid filled capsule, which has a boiling point less than that of steam at the corresponding saturation pressure. When the capsule is exposed to hot condensate, the liquid inside it vapourises. This leads to expansion of the capsule, pushing the valve against the seat closing the trap.
Subsequently when the temperature of condensate surrounding the capsule drops, the vapour within it condenses, causing the capsule to contract and in turn lifting the valve off its seat to allow condensate to pass. These traps are small and light weight and are suitable for use across a wide pressure range.
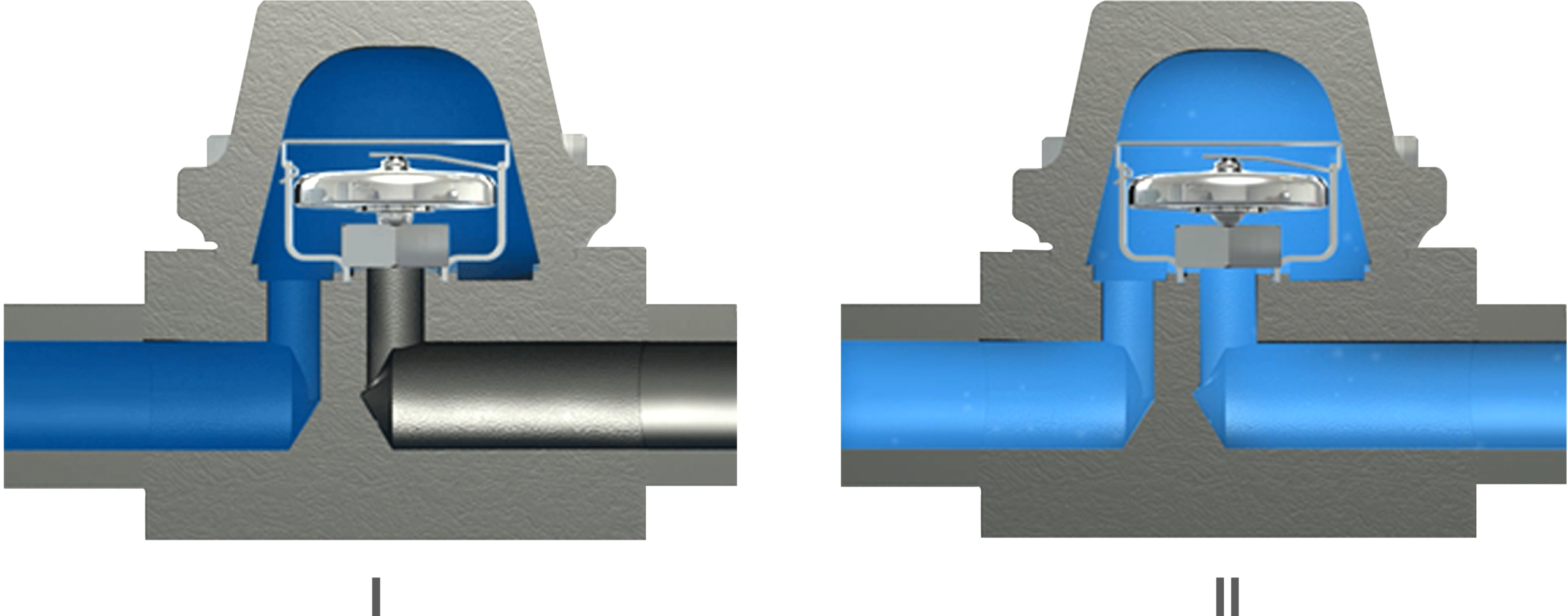
Illustration: How balanced pressure thermostatic steam traps work
- When the capsule is exposed to hot condensate, the liquid inside it vapourises. This leads to expansion of the capsule, pushing the valve against the seat closing the trap.
- Subsequently when the temperature of condensate surrounding the capsule drops, the vapour within it condenses, causing the capsule to contract and in turn lifting the valve off its seat to allow condensate to pass. These traps are small and light weight and are suitable for use across a wide pressure range.
Balanced pressure thermostatic steam traps are typically used to vent out air and non-condensable gases present in the steam system. Air vents should be ideally installed in the distribution network, including at dead ends and on steam using equipment especially with large steam spaces. Additionally, since these steam traps hold back condensate and allow it to be discharged only when it cools down to a specific temperature, they are ideal for steam tracing applications.
Steam tracing is used across various industries to heat products or raw materials to a specific temperature, to maintain their fluid state and enable pumping and distribution. Heating reduces viscosity and prevents crystallisation or solidification. Maintaining a uniform temperature of product / raw material across the entire length of the tracing networks is crucial to prevent choking.
Balanced pressure thermostatic traps ensure that only sub-cooled condensate is discharged, thereby utilizing both latent heat and some portion of sensible heat within the tracing system. This leads to a reduction in the quantity of steam consumed in tracing.
Liquid Expansion Steam Traps
The liquid expansion traps contain a liquid filled capsule which expands when heated. As the fluid expands, it pushes a valve against the seat, closing the trap. As the liquid cools down it contracts opening the trap.
These traps are available with a mechanism, such that the trap can be adjusted to open at the required temperature between 60 and 100°C. These traps can be used to evacuate subcooled condensate and air present in the distribution systems at startup.
Orifice Steam Trap
Orifice traps have no moving parts. Their construction is very simple, essentially consisting of a plate with a very small orifice at the center which facilitates the discharge of condensate and air. As these traps have a very small orifice, they are susceptible to failing closed due to dirt, debris and deposition that clogs the orifice.
The consequences of a plugged trap are serious, since they have a direct impact on plant and personnel safety. Dirt, debris and deposition due to carryover cannot be ruled out in steam pipelines making this trap largely unsuitable for mainline applications. Furthermore, over time, the orifice size erodes during the course of operation, resulting in significant steam losses. The choice of steam trap depends on factors such as the application, the upstream and downstream pressure, and the condensate load. While considering a type of steam trap for a given application, due consideration should be given to whether the steam trap discharges condensate as soon as it is formed i.e. at steam temperature or discharges condensate below the steam temperature i.e. using some portion of its sensible heat within the process.
Additionally, considerations pertaining to the need for air venting, maintenance, cost, capacity and failure modes also need to be looked at while selecting the type of steam trap. The upstream and downstream pressure, and the condensate load. While considering a type of steam trap for a given application, due consideration should be given to whether the steam trap discharges condensate as soon as it is formed i.e. at steam temperature or discharges condensate below the steam temperature i.e. using some portion of its sensible heat within the process. Proper selection and maintenance of steam traps are essential for efficient and reliable steam system operation.
Read more about selecting the right steam trap for your applications