What is condensate recovery factor and why is it an important parameter to monitor
Condensate recovery across plants varies significantly. Even within the same plant the quantum of recovery changes from day to day.
Benchmarking the recovery enables the plant to :
- Evaluate the recovery within the plant on a daily basis, analyse trends and take timely corrective actions in case of any deviations.
- Enables the plant to assess performance against others within the same industry, thereby providing insights into gaps and areas for
improvement.
What is CRF % and why is it an important parameter to monitor
Condensate Recovery Factor (CRF %) is a metric that enables plants to benchmark the performance of the condensate recovery system. It is calculated by dividing the amount of recovered condensate by the amount of total steam generated and is expressed in percentage terms.
Condensate Recovery Factor (CRF) = Total condensate recovered x 100 / Total steam generated
A higher condensate recovery factor signifies better recovery and therefore significant cost savings in terms of fuel and water.
Monitoring the condensate recovery factor is crucial, as it serves as more than just an indicator of the condensate recovery system’s performance. It also reflects the performance of the entire steam system and process efficiency within the plant.
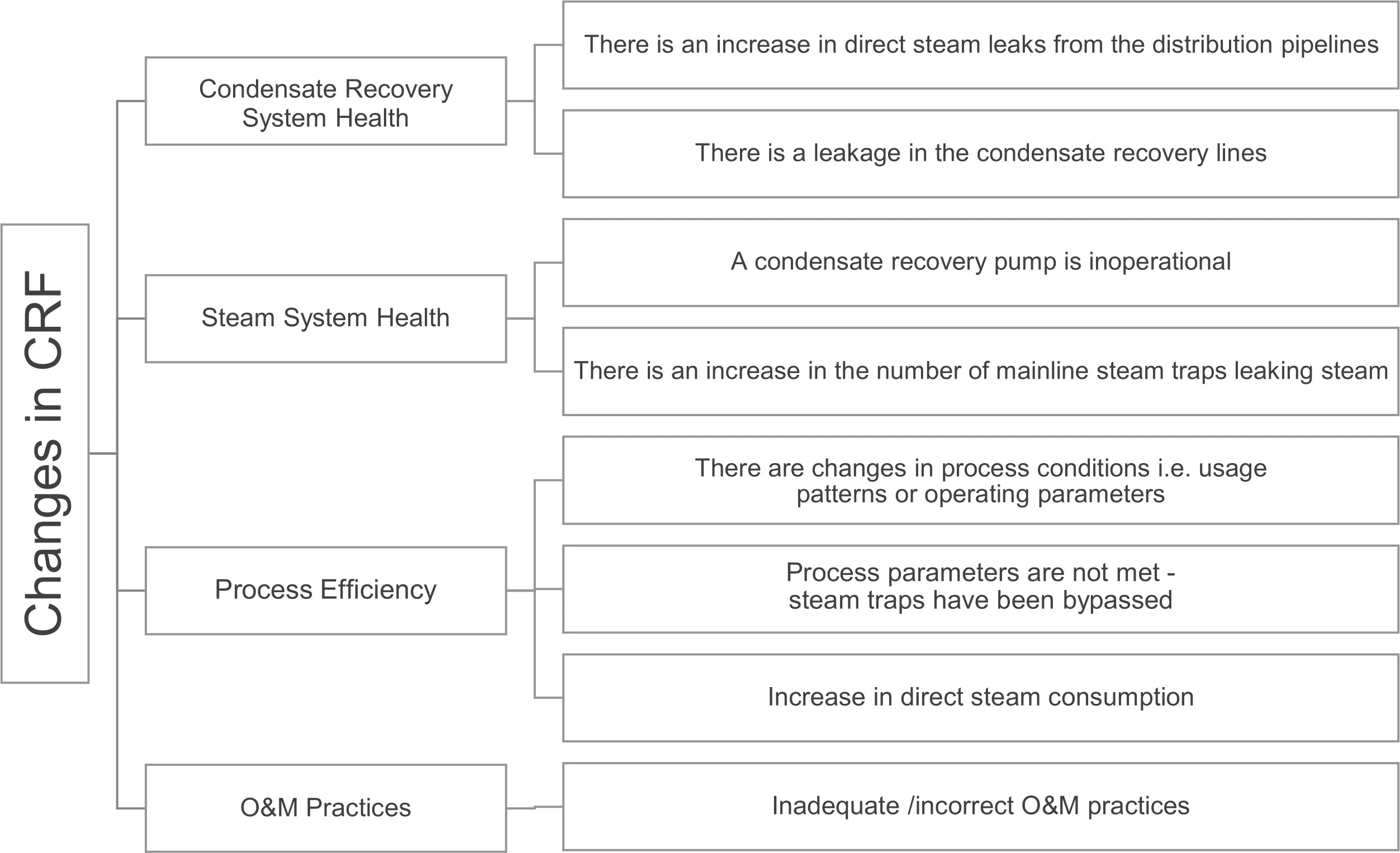
CRF: A metric of process and steam efficiency and O&M practices
For example a drop in condensate recovery can be indicative of an increase in distribution losses due to direct steam leaks or leaking mainline steam traps. It can also be due to process steam traps which are bypassed in order to evacuate condensate from the equipment when operators face issues in achieving process temperatures or gradients. Variations in the recovery factor can indicate changes in
process conditions or operating parameters i.e. usage patterns in blocks / equipment can lead to variations in recovery from the block / equipment.
Downtimes and losses in the condensate recovery system, steam system or at the equipment level also impacts CRF and hence is a good indicator of the effectiveness of operations and maintenance practices in the plant.
Therefore the CRF is a valuable metric for evaluating the overall efficiency and effectiveness of the steam system, as well as the plant’s operational efficiency.
Sustaining CRF%
The condensate recovery factor is not a static figure. It varies on a day to day basis due to various factors within the process and steam system. The graph below represents a typical trend in the recovery factor across a plant. While the absolute figures may vary from plant to plant this trend of dynamic variations is observed across all plants.
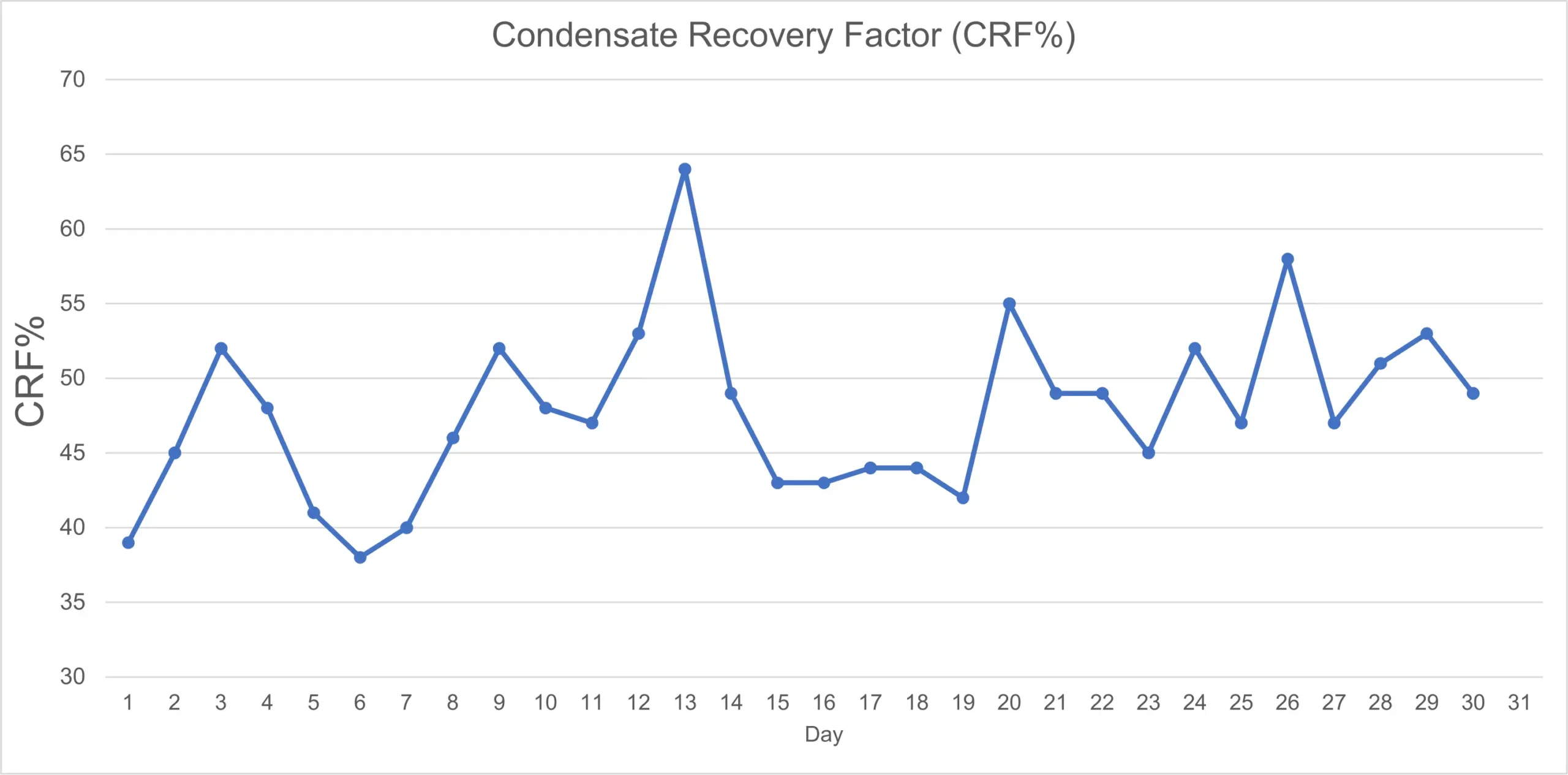
Typical daily variations in CRF, an example
The same data when represented below as a standard deviation curve enables better visualization of what is happening in the plant.
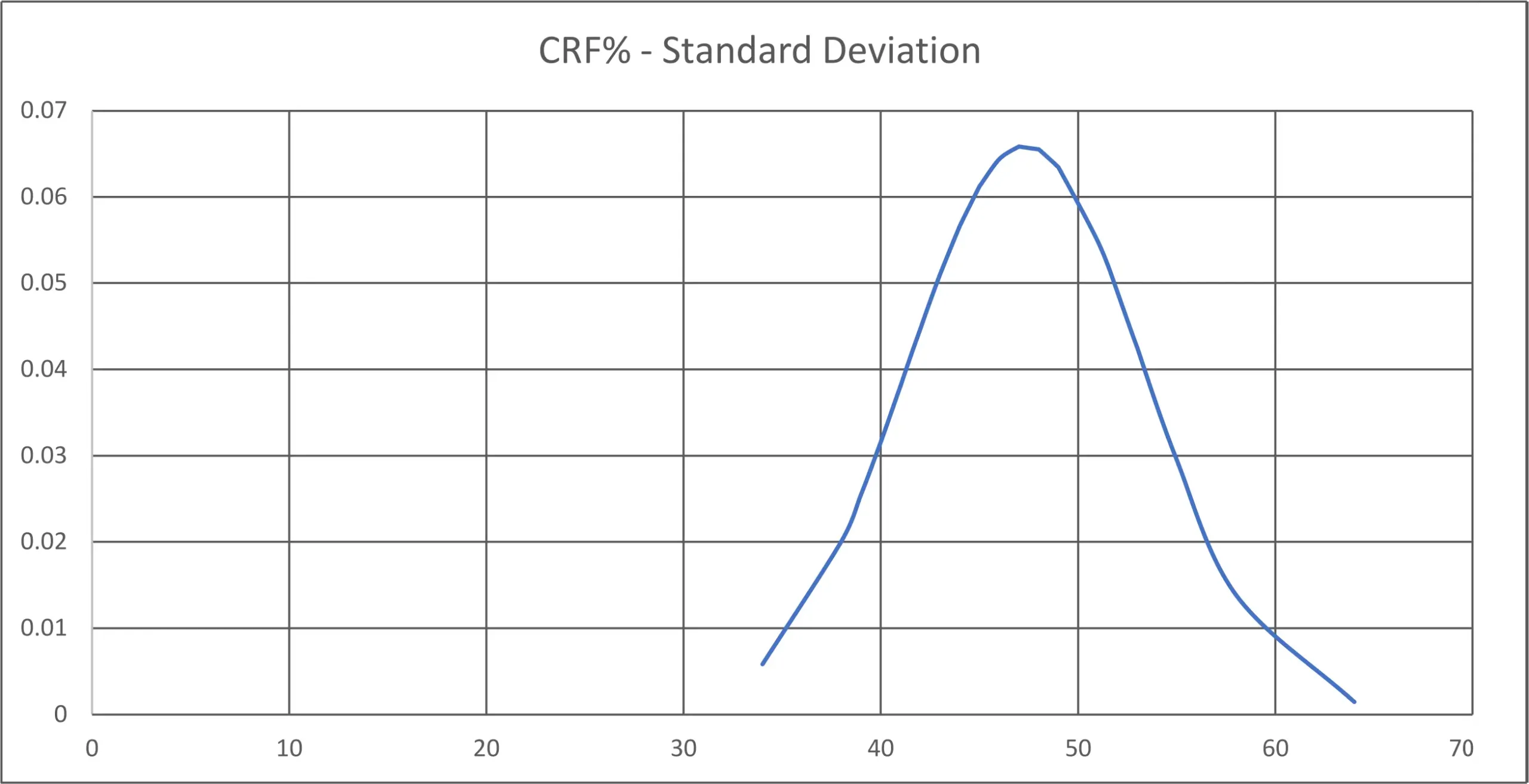
Daily variations in CRF – standard deviation plot
For example it helps to quickly identify the following :
- The mean i.e. the average CRF is 48%.
- The spread of the variations i.e. a wider bell curve indicates higher variability where as a flatter bell curve indicates variations are within a narrow band. For example in this case the CRF varies from 30% to 64%.
- Outliers, unusual or extreme numbers which are one off occurrences for example CRF of 30% and 64% which need to be investigated.
Thus two key issues need to be addressed across plants. First, to improve the overall recovery percentage, of which there is a significant gap against benchmark values across industry segments. The second, sustain the improvement and narrow the band of daily variations in the CRF.
Improving and sustaining the CRF entails the following :
Establish the benchmark CRF for the plant
Establish the direct and indirect steam consumption in the plant as only the indir
ect steam used in the plant is recoverable. This provides an understanding of the improvement possible in the CRF and defines the baseline / benchmark for the plant.
Monitor condensate recovery, make-up water consumption and steam generation:
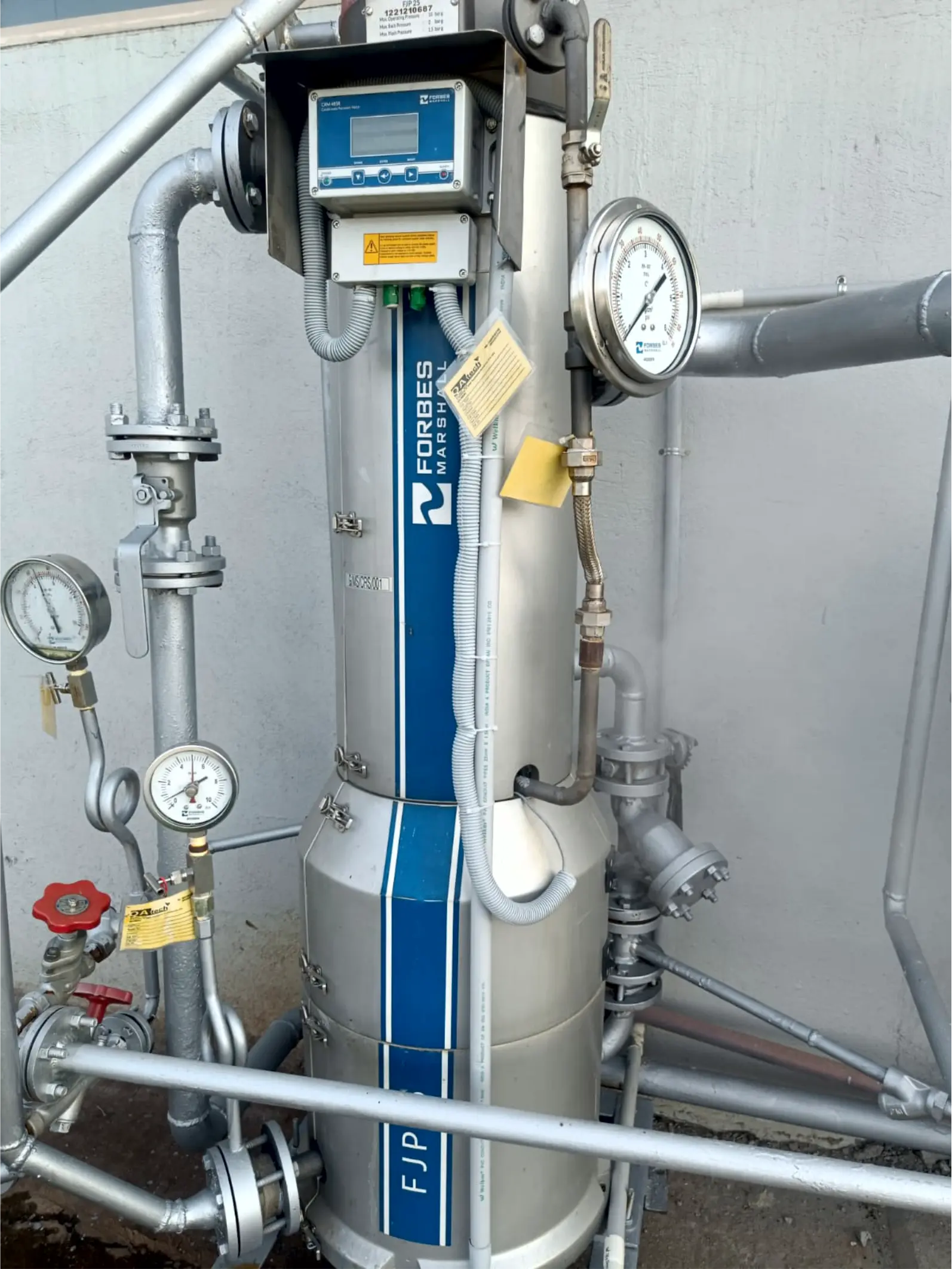
Condensate recovery system with condensate recovery meter
Monitoring is not only crucial to drive improvement but also to sustain performance. Most plants calculate their condensate recovery factor based on a reading of the makeup water consumption. While this gives an indication of the total recovery, it is not enough to pinpoint the cause of deviations in the recovery factor. Furthermore, turbine type meters which are highly prone to errors are commonly installed to measure the makeup water consumption and hence consumption figures cannot be relied on.
It is recommended to install condensate recovery meters to measure the condensate recovery from each pump as well as vortex type steam flow meters to monitor section wise steam consumption and a digital meter to measure makeup water consumption. When condensate recovery is viewed in conjunction with section wise steam consumption it can enable operators to quickly pinpoint the section or equipment which caused the drop in the overall recovery factor thereby facilitating easy troubleshooting and timely rectification.
Investigate the cause of fluctuations / drops in recovery:
A drop in the CRF can occur due to several reasons. Refer Figure 34 of this booklet, which highlights the probable causes of fluctuations / drop in recovery.
Establish SOPs to sustain uptime:
Maintenance SOPs are important to sustain operational reliability of the system. They play a vital role in preventing unplanned downtime, ensuring equipment longevity and sustaining efficient operations. It is important to establish and follow correct operations and maintenance practices to sustain the condensate recovery factor and uptime of condensate recovery systems and steam traps in the plant.
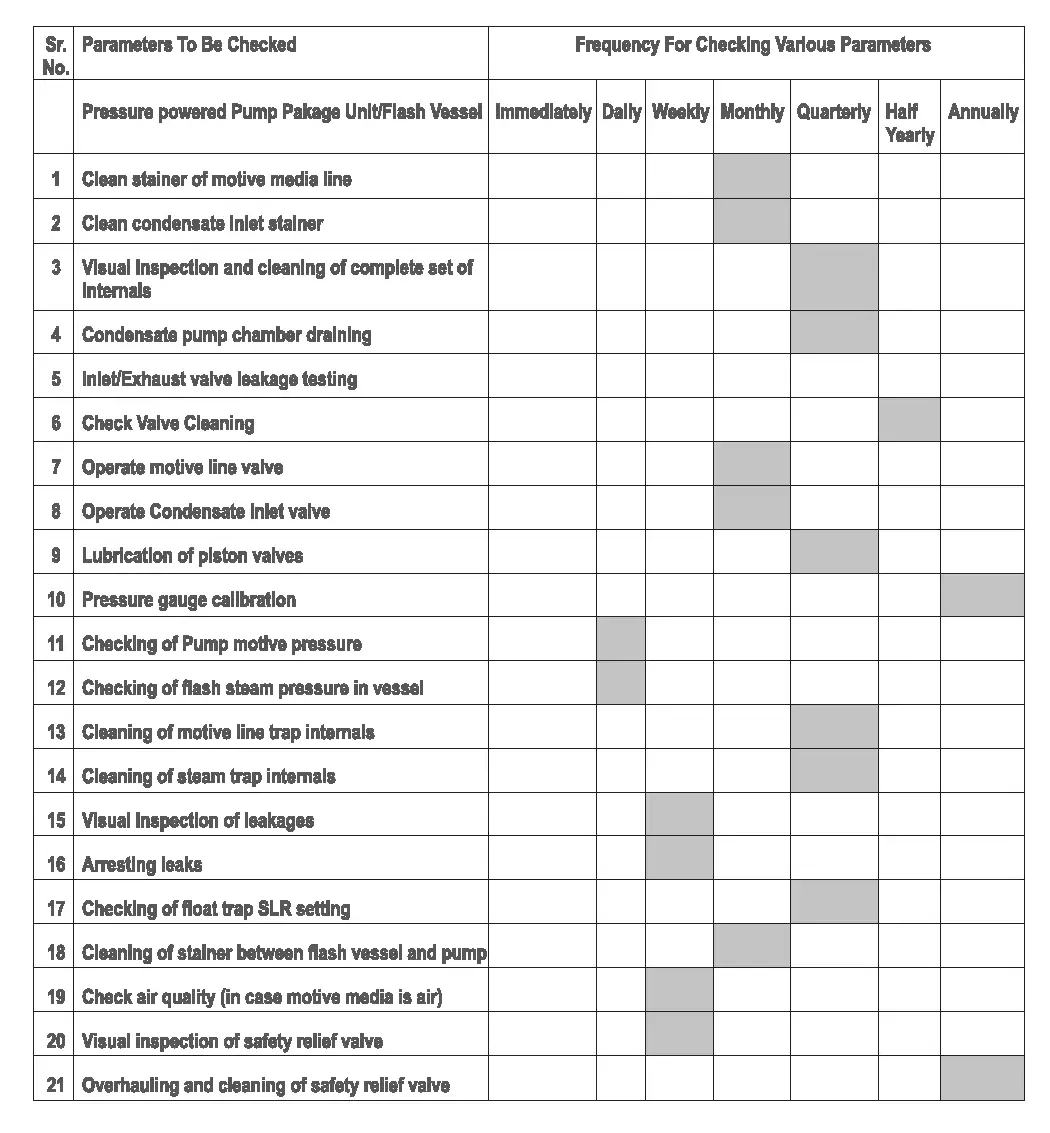
SOP for maintenance of condensate pumps and flash vessels